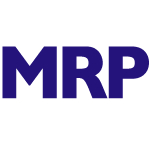
The question is asked in businesses across the planet every day: “Do I have the right level of inventory?”
It reflects the age old business problem of balancing customer service levels with capital efficiency: carry too little inventory and risk a stock out giving a customer a reason to find another supplier, carry too much and tie up capital resources that could be invested elsewhere in the business. Customers do not pay us for materials collecting dust on shelves in a warehouse.
The simple definition of MRP (Material Requirements Planning) is that it is a software algorithm that results in an inventory plan for the purchase, manufacture and transfer of inventory such that inventory levels are minimized and service levels are maximized. We will dig into the definition in more depth shortly but first, let's continue to explore the complexity of the challenge it addresses.
How does Material Requirements Planning work?
MRP is equally applicable to manufacturers and distributors; however, manufacturers must deal with demand at multiple levels of each Bill of Materials (BOM). Inventory requirements for a single item, whether a finished good, subassembly or raw material is likely to be driven by demand from numerous sales orders, work orders, transfer orders and purchase orders. It is quite common to have subassemblies that are used in the BOMs of hundreds of other items while also being sold as an accessory or spare. The supply and demand picture over time for an item like this is especially complicated. Add in multiple stocking points, varying lead times across different items, lumpy customer demand, dynamic schedules, and the task of ensuring a firm has just what it needs where and when, becomes a daunting challenge.
This is where MRP shines. The algorithm takes all of these myriad inputs and formulates a plan based on the answers to these questions:
- How much do I have?
- Where is it?
- When will I receive more?
- How long does it take to get?
- When do I need it?
Other variables exist as well, such as item reorder levels, order up-to levels, and order multiples that temper the plan, but ultimately MRP generates a list comprised of three order types: Purchase Orders, Work Orders and Transfer Orders. Each order identifies the site (in the case of a transfer order that includes a source site and a destination site), item, quantity, order date and due date.
Think of the plan as valued business advice. Execute the plan as specified, and you’ll have the items you need in the quantities required, when required. Fail to execute the plan and risk stock-outs, disgruntled customers, and lost opportunities and sales.
What happens when the plan is executed (i.e., planned orders are turned into actual orders) and then a customer cancels a sales order or moves a scheduled date into the future? For example, a purchase order may have been communicated to a supplier, and you are now waiting for delivery or a work order has been scheduled in manufacturing. This is where MRP exceptions come into play. The MRP exceptions function looks at actual orders and presents advice on how to proceed. This advice may be to move the due date in, out, or cancel the order altogether.
Then, there is the challenge of demand variability within an item’s lead time. How do we handle fluctuating and unpredictable demand patterns especially once the replenishment order has been issued?
MRP exceptions can help with this; however it is not always possible to accommodate its advice. An additional way to tackle this problem is through the reorder levels and order up to levels that are set for each item. MRP generates a replenishment order for any item whose availability will drop below its reorder level at some point in the future. The order quantity is influenced by many factors, including actual demand, but the reorder level and the order up to level set an availability range planned by the MRP system. When availably is projected, at some point in the future, to drop below the reorder level, MRP plans a replenishment order, the quantity of which will return the availability to the greater of the order up to level or actual demand.
Reorder levels and order up to levels are examples of "good" buffers. These are buffers that moderate the MRP system's planning and that we set knowingly because we recognized that every item has some variability of demand and supply that is not knowable. Short of getting the lead time of an item down to 0, setting an appropriate reorder level and order up to level is best practice. An MRP utility can analyze past requirement patterns for each item and provide advice for the item's reorder level and order up to level.
Incidentally, "bad" buffers are what firms that do not have MRP maintain. They are usually set arbitrarily high for fear of a stock out and because the firm lacks the capability to generate a comprehensive time-phased inventory plan that accounts for aggregated supply and demand at all levels of the BOM.
What are the Benefits of Material Requirements Planning?
The biggest benefit to using MRP is not that it helps ensure purchase orders, work orders and transfer orders are created with the proper quantities and dates, so that service levels are maximized and capital tied up in inventory is minimized. That sounds like enough, though, doesn’t it?
Using MRP properly, your system is now handling the repetitive, tedious and transactional inventory planning work. Your planners and buyers are freed up to perform the tasks that computers cannot. Buyers who are not constantly responding to inventory crises can work on negotiating with suppliers, seeking out new sources of supply, and ensuring quality and delivery standards are met. Shop floor supervisors can turn their attention to improving shop quality and efficiency.
With MRP, your business transforms from one that is reactionary and responding to the emergency of the hour to one that is proactively working to improve, and grow profitability.
As with any tool, MRP must be used and maintained properly and become an integral part of the culture. Settings on items become critical as do the accuracy of bills of material and dates on all inventory orders. Vigilance on the part of everyone who touches item settings, bills of material, transfer orders, purchase orders, work orders and sales orders is paramount.
The advice that MRP generates is only as useful as the quality of its inputs. Organizations that embrace the discipline of ensuring that the information that influences MRP is kept current will reap the benefits outlined here, and employees will come to a much more rewarding and pleasant workplace each day.
Is MRP a panacea for the inventory planning challenges your firm faces? Not quite. It must be applied to the correct problem. Not all items should be planned by MRP. Next, we will explore the problems that MPS (Master Production Scheduling) addresses, and the items that should be planned through it.
What is MRP (Material Requirements Planning)?
This is the first in a series of articles to explore Inventory management, EOQ (Economic Order Quantity), Inventory planning, Distribution MRP or DRP (Distribution Requirements Planning), MPS (Master Production Schedule), ISO certifications, how to use MRP, and how to choose the best MRP software.