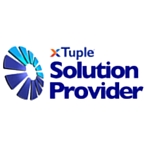
Stories abound about business improvement and ERP systems implementations going terribly wrong. Research shows that it normally is not the ERP system at fault, but rather some other factor not well considered during implementation. Lack of executive support, faulty process definition, inadequate training, a lack of organizational readiness or misunderstanding the workflows across the value chain are some of the reasons seen for implementation difficulty.
Using a standard methodology to implement ERP systems goes far in eliminating the chances of failure. We utilize a methodology to manage our implementations, which helps to ensure all the elements required for successful implementation are considered at the appropriate time.; The methodology orders the activities in a logical and memorable way through the use of the ‘Seven M's’. This model holds that Man, Money, Machines, Methods and Motivations represent the complete set of means for affecting a change to an organization which is then Measured and Managed.
Each of the seven M’s is a lever for driving change and virtually any change will require that each lever be adjusted or controlled in some manner or another. A new ERP system (Machine) is not valuable without the supporting processes and procedures (Methods) or the training (Man) to use it. Projects fail due to lack of control over one or more of these means during one or more stages of a project.
In this and the blog entries to come later, we’ll dive into some detail about each of the Seven M’s. This issue will highlight Manage and Money and we’ll detail the other M’s in future blogs.
MANAGE:
Managing involves integrating each element (Money, Man, Machine, etc.) into a cohesive and effective plan. It is the project management aspect that links and coordinates the separate activities to achieve a common goal, and involves evaluating and controlling the risks associated with the project. The key activities to initiate the project are:
- Analyzing the market (customers, users, etc.) and identifying the need
- Describing the customer requirements in discrete and measurable terms
- Compiling requirements by end user
- Appointing an individual with the responsibility of managing the activities required to achieve this solution and to coordinate and direct the efforts of the team
- Define strategy for achieving benefit
- Prepare work break-down structure
- Determine resource requirements
- Schedule overall project
MONEY:
This involves the financial aspects of managing the project, such as investments, returns, benefits, costs, budgets, financing, cash flows, and financial risk. It begins with developing a value proposition as the economic rationale for pursuing an investment. The term ‘value’ is used to recognize that qualitative benefits such as employee or customer satisfaction should also be considered in the investment rationale as should the long-term objective of increasing shareholder returns. This includes:
- Outlining all costs and benefits associated with the ERP systems implementation
- Providing convincing evidence that the required investment is beneficial to the company in terms of return on investment, strategic positioning, etc.
- Identifying where anticipated benefits are realized in the business and over what timescales
- Understanding the risks associated with undertaking the project and weighing their effect in terms of likelihood and consequence
- Outlining plans for mitigating these risks with convincing arguments that the resulting return on investment still meets the firm’s objectives
Man, Machines, Methods, Motivations, and Measure are up next.