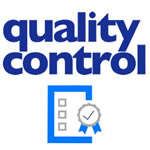
Inspection and Testing During Product Lifecycle
Do you need to meet standards of excellence and document regulatory and/or quality compliance? Want to easily manage and/or improve non-conformance with corrective and preventative actions? We're talking about ISO (International Organization for Standardization) and FAI (First Article Inspection) for your specific industry, important for both manufacturers and distributors.
From purchased product to production to distribution and customer service, xTuple Quality Control add-on is a suite of tools to help you do just that.
Extensions and add-ons are powerful additions to xTuple's core enterprise resource planning (ERP) offerings, and lately, a number of customers have asked about our Quality Control package.
Questions include: what is it, how does it work, does it track costs... just to name a few.
Quality Control gives users the ability to integrate routines into their workflow for improved efficiency and document requirements for compliance. Users setup their own Quality Specifications, Plans, Dispositions and Documents to meet their needs and industry standards. The system captures all costs associated with rework or scrap disposition of a production run for more complete insight into true production costs.
Quality is a powerful tool that allows you to effectively manage costs, efficiency and streamline workflow, and if you care about the bottom line, this package gives you the visibility you need.
Interested in learning more about what features are included in the xTuple Quality module and how your company can benefit? Tune in! We've got a webinar for that!
WEBINAR: Register for Introduction to Quality Testing and Workflow
Thursday, February 1st at 4:00 p.m., Eastern Time (GMT-05:00-US & Canada)
Who uses xTuple Quality Control, and why?
Quality is of paramount concern for food and beverage, medical, aerospace, automotive or the general manufacturer. The QC add-on introduces new quality concepts into multiple key areas of xTuple ERP.
- Quality Test Specifications — instructions and item requirements for inspections or tests to be conducted
- Quality Test Plans — define what test specifications are to be applied on which items and at what interval or frequency; xTuple can automatically create and assign Testing Documents to the correct users
- Quality Test Dispositions — define the current status of the Quality Test and the item being tested, and whether the item is in testing, released for further use, or has failed a test and requires the user to scrap, quarantine or rework the item; appropriate notifications of non-compliance are automatically routed to key stakeholders
- Quality Test Documents — the actual execution document which identifies that a test is required and, specifically, what needs testing as well as the detailed test results based on actual observation or measurements; used extensively in reporting and statistical analysis